Share
Composite Moulding is the Future of Lightweight Engineering
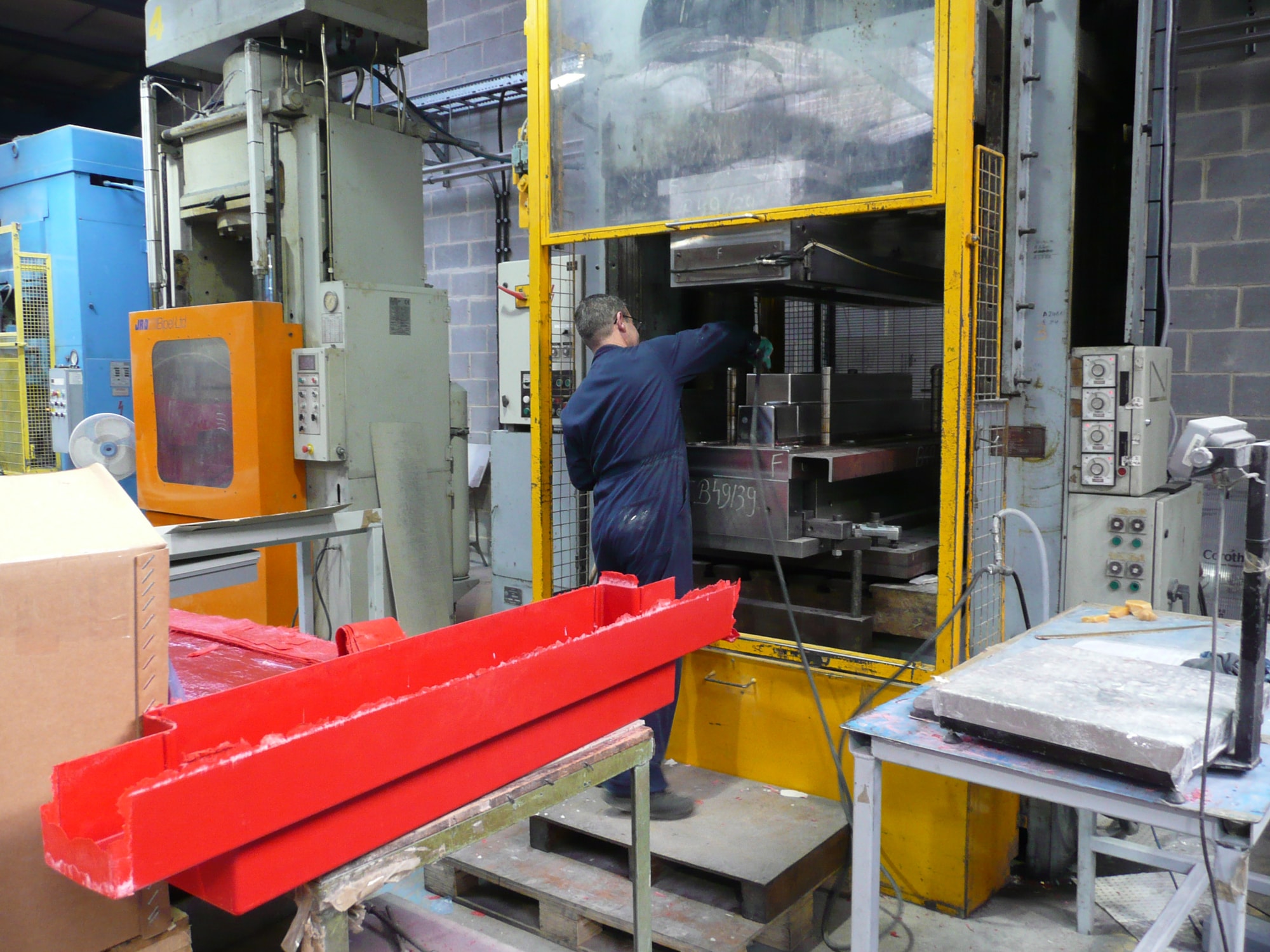
In a world focused on efficiency, sustainability, and performance, lightweight engineering has become a top priority across industries. From automotive and aerospace to rail and defence, reducing component weight without compromising strength is a game-changer. At Talisman Group, we believe composite moulding is key to unlocking this future.
What Is Composite Moulding?
Composite moulding involves forming components from reinforced materials, typically combining a polymer base with fibres like glass or carbon. The result is a lightweight part with exceptional strength and durability.
At our Crewkerne facility, we specialise in compression moulding, a process where SMC (Sheet Moulding Compound) or BMC (Bulk Moulding Compound) is placed into a heated mould cavity, compressed under pressure, and cured to form solid, high-performance parts.
Unlike some traditional thermoset moulding materials, SMC and BMC are not typically preheated before moulding. Preheating these materials can burn off important inhibitors, which are essential to controlling the curing profile and ensuring the material flows and cures correctly.
This process is ideal for producing complex, strong, and consistent parts in medium-to-high volumes.
Why Lightweight Engineering Matters
Reducing component weight offers key benefits:
- Improved fuel efficiency in vehicles and aircraft
- Lower energy consumption in rail and transport
- Increased payload capacity in logistics and defence
- Reduced emissions and environmental impact
- Easier handling and installation during assembly
Across industries, every gram saved can mean big gains in performance, cost, and sustainability.
Benefits of Composite (Compression) Moulding
Here’s why manufacturers are turning to composite moulding:
- High strength-to-weight ratio
- Dimensional stability and tight tolerances
- Excellent chemical and corrosion resistance
- Works with a range of advanced thermoset materials
- Supports complex part design with minimal secondary processing
In conventional thermoset moulding (such as Phenolic, Melamine, and Urea moulding), preheating granules or biscuits is used to improve flow characteristics and aid curing. However, for SMC and BMC, direct mould loading ensures that their chemical inhibitors remain intact during the forming process.
Where It’s Making an Impact
We deliver composite moulded components for a range of applications, including:
- Rail interiors and exterior panels
- Automotive underbody parts and housings
- Electrical and industrial enclosures
- Structural components for defence equipment
These parts often need to perform under pressure, literally, and composite moulding gives them the strength and resilience to do just that.
The Talisman Group Edge
As a unified organisation with decades of experience, Talisman Group offers deep technical expertise and fully integrated services from tooling and design through to production and assembly.
Our dedicated composite moulding site in Crewkerne allows us to deliver:
- Scalable production
- Fast tooling turnaround
- Application-specific material recommendations
- Ongoing technical support
We’re proud to help customers innovate, reduce weight, and improve performance without compromising on quality.
Let’s Build Lighter, Together
As demand grows for stronger, smarter, and lighter materials, composite moulding will continue to play a central role in engineering innovation.
Ready to explore light weighting for your next project?
Get in touch with our team to find out how we can help.